What is Mokuhanga
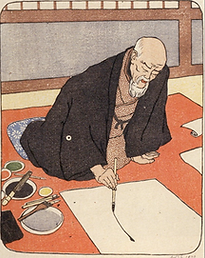
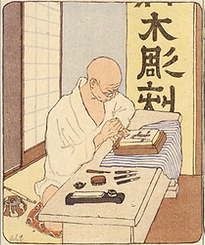
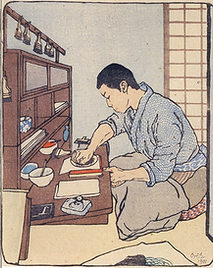
heres a brief explanation of the process of creating a woodblcok print
In Japanese, moku means "wood" and hanga means "print," making mokuhanga the term for Japanese woodblock printmaking. Originally developed in China, woodblock printing was refined and mastered in Japan. Early prints were created by carving key outlines into woodblocks, with artists painting on top to produce full-color images. However, it was during the Edo period that the art of multi-colored printing was perfected, making it accessible to the general public.
Today, very few masters still practice this craft. The process traditionally begins with an artist's drawing. This design is then transferred as a hanshita (a lined design ready to be pasted) onto the woodblock for carving. Typically, this step is hanshita is produced by the workshop producing the print, though sometimes the artist will do this themselves. traditionally a very thin piece of paper is placed over the design, which is then carefully traced, adding in any recurring details or refining messy lines according to the artist's instructions. Today, for reproduction prints, the hanshita can be made digitally, offering greater fidelity to the artist's brushstrokes. Once the design is ready, it is pasted onto the woodblock, and the back of the paper is rubbed with water to remove the excess paper, revealing the design. Occasionally, a touch of camellia oil is used to increase the paper's transparency, but this should be done just before carving, as the oil may cause the paper to detach over time. The lines are carved on both sides, and the waste wood is cleared out, leaving a raised design on the surface.
This carved block is known as the Omohan or Daiban (key block). After the glue and paper are washed off, the block is ready for printing. Sumi ink is applied to the block, usually with a marubake (a round brush made from horsehair), and impressions are taken by placing paper on top of the block and rubbing the back with a baren. Multiple impressions are made, and colors are gradually added by masking off certain areas of the block.
The process for each color follows the same steps as the key block carving. Once carving for all color blocks are completed, the block is ready for printing.
The blocks are then sent to the next person in the process: the printer. The printer applies pigments to each block in succession, using different types of barens—ranging from coarse to fine—depending on the texture and delicacy of the carving. A registration system, known as kento, ensures alignment of each printed layer. The carver creates kento by carving an L-shaped notch (kagi) in the lower-right corner and a flat line (hikitsuke) along the bottom edge.
Before printing, the paper is carefully wetted and maintained at a constant moisture level throughout the process to avoid swelling or shrinking, which would lead to misregistration. The final key figure in this process is the publisher, who organizes, commissions and compensates the craftspeople involved in the production of the print. Today, many printmakers take on multiple roles, but in the traditional system, these roles were clearly defined: the artist, the carver, the printer, and the publisher each had their distinct responsibilities. While I greatly respect multidisciplinary artist-producers, I choose to follow the path of the craftsperson.
画師・彫師・摺師・版元

Stylistic Categories
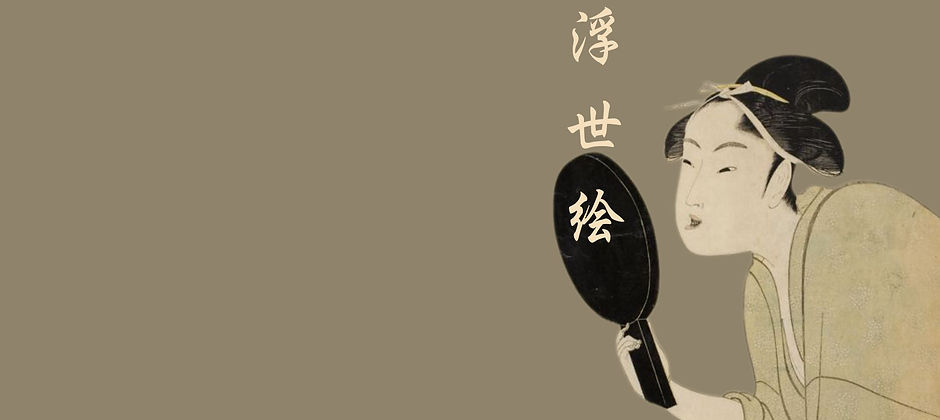.jpg)
UKIYO-E
Ukiyo-e referes to a Japanese art style of Mokuhanga originating in Edo in the early 1600s. It translates to "pictures of the floating world" and depicts numerous themes such as pop-culture of the time, kabuki actors beautiful women and landscapes.
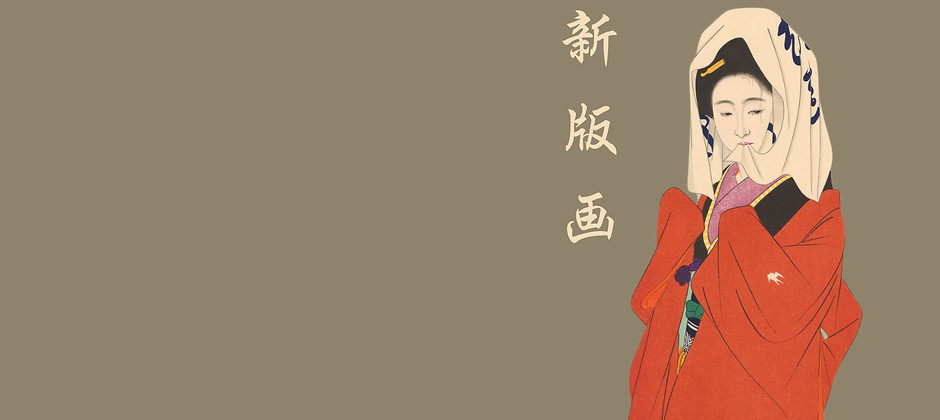
Shin Hanga
Shin-hanga is a Japanese art movement pioneered by Shōzaburō Watanabe in the early 20th century. The movement was developed off the back of the ukiyo-e tradition but used contemporary western artistic practices such as perspectives and shadows. They are a much more complicated production using layering to create deep and intricate colours in the final print along side a number of other techniques such as goma-zuri. While retaining the clasical production structure of traditional ukiyo-e production.
.jpg)
SOSAKU HANGA
creative prints
These are prints created in the present or recent past, encompassing various styles and themes that reflect current ideas and trends, with a focus on innovation. There have been many suggested names for current trends in printmaking such as 'Reiwa Hanga' 'Gendai ukiyo-e' and 'Neo Ukiyo-e'

CONTEMPORARY PRINTS
These are prints created in the present or recent past, encompassing various styles and themes that reflect current ideas and trends, with a focus on innovation. There have been many suggested names for current trends in printmaking such as 'Reiwa Hanga' 'Gendai ukiyo-e' and 'Neo Ukiyo-e'
Within all broad categories there are a myriad of genres and sub genres describing the subjects and the style of the images. categories can be mixed and matched to best describe any image such and an 'ukiyo-e fukega' (a landscape in the ukiyo style).